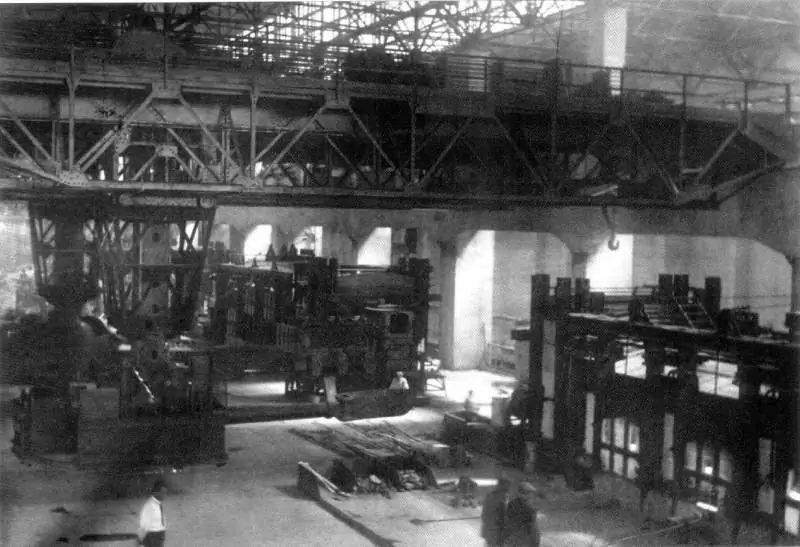
Recurs estratègic
És difícil sobreestimar la producció d’acer d’alta qualitat per al complex militar-industrial en condicions de guerra. Aquest és un dels factors més importants en l'èxit dels exèrcits al camp de batalla.
Com ja sabeu, els metal·lúrgics de Krupp van ser dels primers a aprendre a produir acer d'alta qualitat per a armes.
Els alemanys van adoptar el procés de fabricació de Thomas a finals del segle XIX. Aquest mètode de fosa d’acer va permetre eliminar les impureses de fòsfor del mineral, cosa que va augmentar automàticament la qualitat del producte. Les armadures i armes d'acer d'alta qualitat durant la Primera Guerra Mundial sovint asseguraven la superioritat dels alemanys al camp de batalla.
Per organitzar aquesta producció, es necessitaven nous materials refractaris que revestissin les superfícies interiors dels forns. Els alemanys van utilitzar els últims refractaris de magnesita per al seu temps, resistint temperatures de més de 2000 graus. Aquestes substàncies amb major refractarietat es basen en òxids de magnesi amb petites mescles d’òxids d’alumini.
A principis del segle XX, els països amb tecnologies per a la producció massiva de refractaris de magnesita podien permetre’s la producció de cuirasses i armes d’alta qualitat. Això es pot comparar amb un avantatge estratègic.
Els materials anomenats altament refractaris que suporten temperatures de 1750 a 1950 graus eren més baixos en termes de resistència al foc. Es tracta de refractaris dolomítics i amb molta alúmina. Els materials refractaris de gres, semiàcids, quars i dinas poden suportar temperatures de 1610 a 1750 graus.
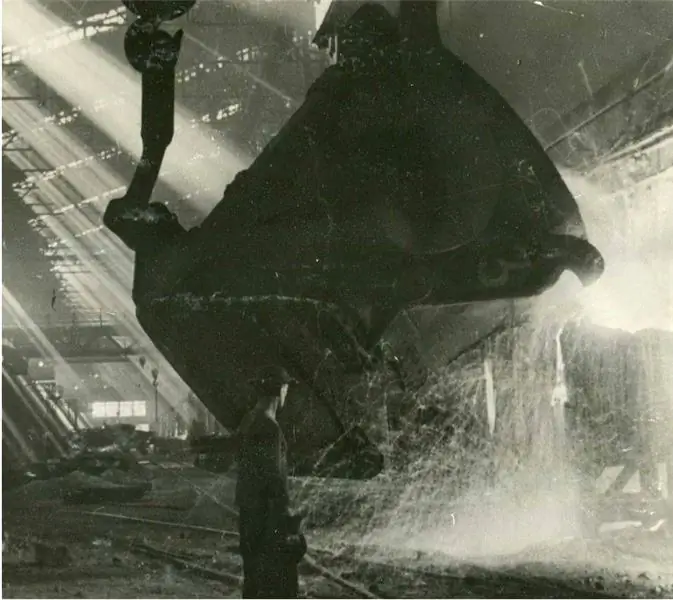
Per cert, les tecnologies i els llocs per a la producció de refractaris de magnesita van aparèixer per primera vegada a Rússia el 1900.
El maó refractari de magnesita Satka el 1905 va rebre una medalla d'or a l'Exposició Industrial Mundial de Lieja. Es va produir a prop de Chelyabinsk, a la ciutat de Satka, on hi havia un jaciment de magnesita únic.
El mineral periclasa, a partir del qual es fabricaven els refractaris a la fàbrica, era d’alta qualitat i no requeria un enriquiment addicional. Com a resultat, el magnesita refractari de Satka era superior als seus homòlegs de Grècia i Àustria.
Reduir la bretxa
Malgrat el maó de magnesita bastant d'alta qualitat de Satka, fins als anys 30, els principals refractaris dels metal·lúrgics soviètics eren materials dinas d'argila. Per descomptat, aconseguir una temperatura elevada per a la fosa d’acer d’armes no va funcionar; el revestiment de l’interior dels forns de llar obert es va esfondrar i va requerir reparacions extraordinàries.
No hi havia prou maó Satka i, en el període postrevolucionari, es van perdre les principals tecnologies de producció.
Al mateix temps, els europeus van seguir endavant, per exemple, la magnesita austríaca Radex es distingia per una excel·lent resistència al foc.
La Unió Soviètica va comprar aquest material. Però era impossible obtenir un analògic sense un secret de producció. Aquest problema el va assumir un graduat de la Universitat Tècnica Estatal de Moscou. N. E. Bauman Alexey Petrovich Panarin. A la planta Magnet (antiga combinadora Satka) el 1933 va dirigir el Laboratori Central de Plantes. I cinc anys més tard, va llançar la producció en massa de refractaris periclasa-cromita o cromagnesita per a forns de xemeneia oberta.
A la planta metal·lúrgica de Zlatoust i al martell i falç de Moscou, el refractari de Panarin va substituir els dines obsolets.
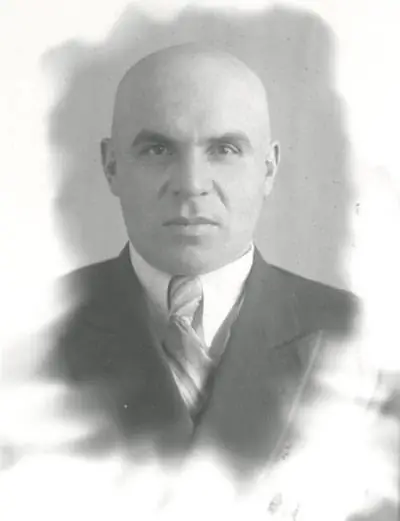
La tecnologia, desenvolupada al laboratori de "Magnezit" durant diversos anys, consistia en una composició i una mida de partícula especials.
Anteriorment, la planta produïa maons convencionals de crom-magnesita, formats per mineral de ferro de magnesita i de crom, en una proporció de 50/50. El secret revelat pel grup de Panarin era el següent:
“Si s’afegeix mineral de cromita en grans granulomètrics gruixuts amb un contingut mínim de fraccions inferiors a 0,5 mm a una càrrega de magnesita normal, fins i tot amb una addició del 10% d’aquest mineral, l’estabilitat tèrmica del maó augmenta bruscament.
A mesura que augmenta l'addició de mineral de cromita de granulometria gruixuda, l'estabilitat del totxo creix i arriba a un màxim a una proporció determinada de components.
La cromita per al nou refractari es va prendre a la mina de Saranovskoye i es va continuar explotant la periclasa a Satka.
En comparació, un maó de magnesita "prerevolucionari" normal suportava temperatures entre 5 i 6 vegades inferiors a la novetat de Panarin.
A la planta de fosa de coure de Kirovograd, el crom-magnesita refractari al sostre d’un forn reverberatori va suportar temperatures de fins a 1550 graus durant 151 dies. Anteriorment, els refractaris d’aquests forns s’havien de canviar cada 20-30 dies.
El 1941 es va dominar la producció de refractaris a gran escala, cosa que va permetre utilitzar els materials en grans forns d'acer a temperatures de fins a 1800 graus. Una important contribució a això va ser realitzada pel director tècnic de "Magnezit" Alexander Frenkel, que va desenvolupar un nou mètode de subjecció del material refractari als sostres dels forns.
Refractaris per a la victòria
A finals de 1941, els metal·lúrgics de Magnitka van aconseguir allò impensable: per primera vegada a la història van dominar la fosa d’acer blindat per a tancs T-34 als principals forns pesats.
El principal proveïdor de refractaris per a un procés tan important va ser Satka "Magnezit". No cal parlar de les dificultats de la guerra, quan un terç dels treballadors de la fàbrica van ser cridats al front i l’Estat va exigir que es complís massa el pla. Tot i això, la planta feia la seva feina i Panarin el 1943
"Per dominar la producció de productes altament refractaris a partir de matèries primeres locals per a la metal·lúrgia ferrosa"
va ser guardonat amb el premi Stalin.
El 1944, aquest metal·lúrgic-investigador desenvoluparà una tecnologia per a la producció de pols de magnesita d'alta qualitat "Extra". Aquest producte semielaborat es va utilitzar per preparar un refractari premsat utilitzat en la producció especialment important d’acer blindat en forns elèctrics. El límit de temperatura per a aquests refractaris va arribar als 2000 graus.
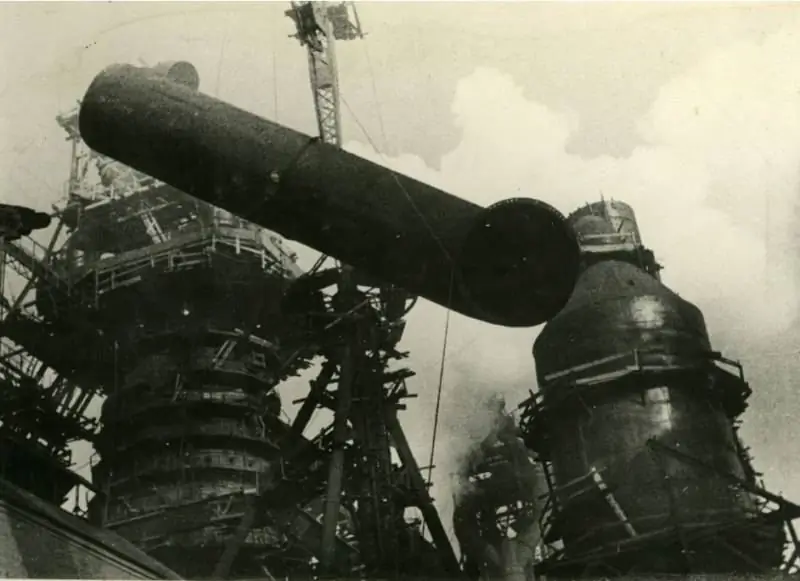
Però no s’ha de suposar que l’exemple d’una planta Magnezit generalment reeixida s’estenia a tota la indústria refractària de la Unió Soviètica.
Es va desenvolupar una situació particularment difícil a l’Ural, on pràcticament tot l’edifici de tancs del país va ser evacuat el 1941-1942.
Les plantes metal·lúrgiques de Magnitogorsk i Novotagilsk es van reorientar a la producció d'armadures, subministrant productes a la planta de tancs Sverdlovsk Uralmash, Chelyabinsk "Tankograd" i Nizhny Tagil núm. 183. Al mateix temps, les plantes metal·lúrgiques tenien la seva pròpia producció de refractaris a partir de matèries primeres locals..
Per exemple, a Magnitka, la planta de dinas-chamotte produïa 65-70 mil tones de maons a l'any. Això no va ser suficient, fins i tot per a les seves pròpies necessitats, per no parlar dels subministraments a altres empreses.
Les primeres dificultats van sorgir quan les fàbriques de tancs van començar a construir els seus propis forns de calefacció i tèrmics. La metal·lúrgia dels urals amb prou feines tenia prou refractaris i, per tant, la producció del casc de les fàbriques de tancs requeria materials d’alta qualitat per revestir els forns.
Aquí no es va parlar de cap refractari de cromagnesita: aquest material era escàs, i fins i tot s’exportava a canvi d’un préstec d’arrendament americà. Almenys això s’esmenta en diverses fonts. Els historiadors dels Ural escriuen que la cara cromagnesita de Panarin podria sortir a l’estranger a canvi d’escasses ferroaliatges per a armadures de tancs. Però encara no hi ha proves directes.
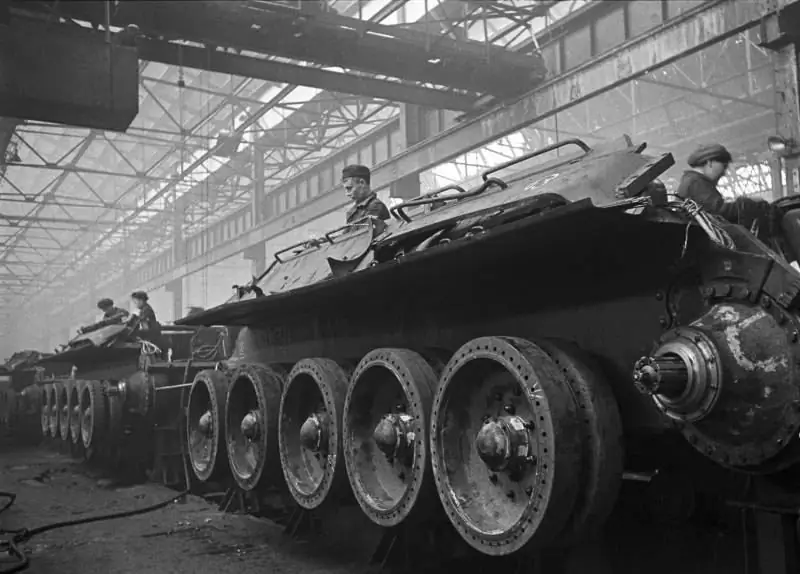
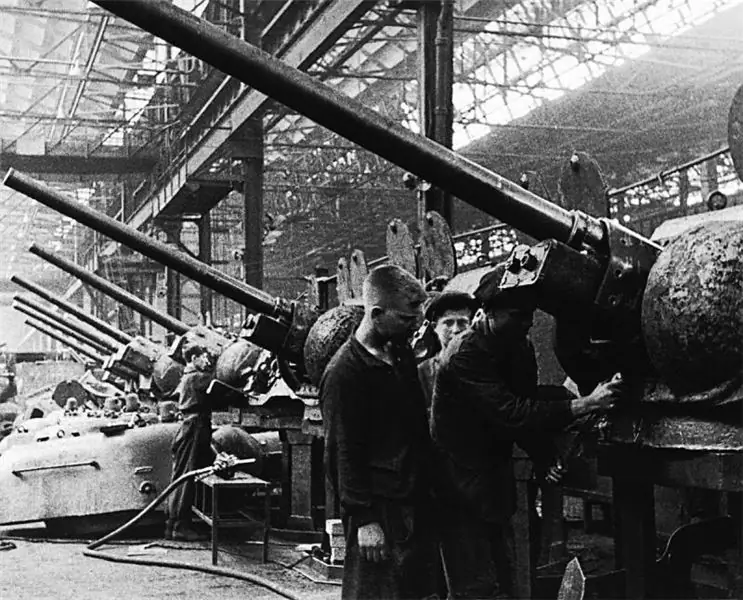
Les fàbriques de tancs depenien principalment de material refractari dinas produït per la planta de Pervouralsk. Però, en primer lloc, es produïa només 12 mil tones al mes i, en segon lloc, els metal·lúrgics van ocupar la major part del lleó.
L'expansió de la producció a la planta de Pervouralsk va anar molt lentament. I a mitjans de 1942, només van aparèixer 4 nous forns. La resta o no estaven preparats o, en general, només existien en projectes.
Els refractaris per a forns de xemeneia oberta de fàbriques de tancs sovint eren de mala qualitat, no en la seva totalitat ni en el moment equivocat. Només per a la reparació de forns Uralmash al quart trimestre de 1942, es van requerir 1035 tones de maons resistents al foc i només es van rebre unes 827 tones.
El 1943, la botiga oberta d’Uralmash, en general, gairebé es va aturar a causa de la manca de refractaris per reparar.
La qualitat dels refractaris subministrats al llarg de la guerra deixava molt a desitjar. Si en condicions normals el maó dinas del forn de llar obert podia suportar 400 escalfades, aleshores en temps de guerra no superava les 135 calors. I al març de 1943, aquest paràmetre havia baixat a 30-40 escalfaments.
Aquesta situació demostra clarament com la manca d’un recurs (en aquest cas, refractari) pot frenar greument la tasca de tota la indústria de la defensa. Tal com escriu a les seves obres el candidat a les ciències històriques, Nikita Melnikov, al març de 1943, tres forns oberts d’Uralmash encara es van aturar i van realitzar un cicle complet de treballs de reparació. Es van necessitar 2346 tones de dines, 580 tones de xamota i 86 tones de magnesita escassa.
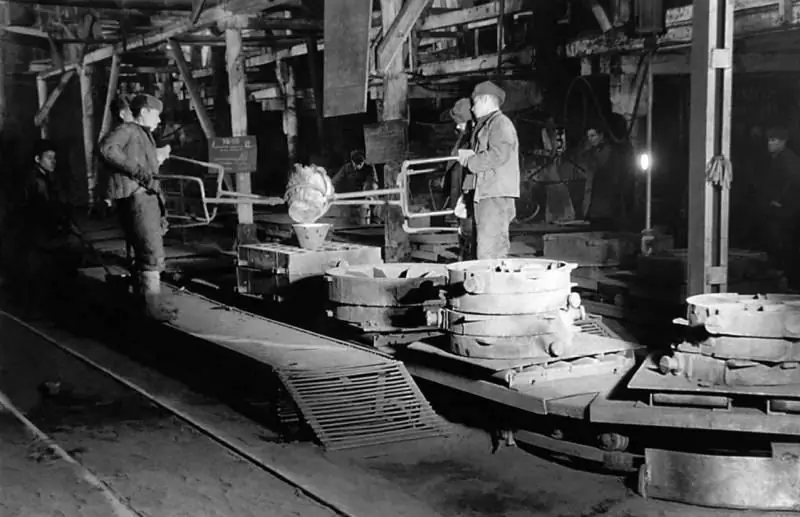
A mitjan 1942, a la planta de tancs núm. 183, la situació es desenvolupava de manera similar: la producció d'acer es va quedar enrere del muntatge mecànic. I vam haver de "importar" els cascos T-34 d'Uralmash.
Una de les raons va ser la manca de productes refractaris per a la reparació de forns de llar oberts, que a la primavera de 1942 treballaven al límit. Com a resultat, només 2 de cada 6 forns de llar oberts estaven en funcionament a la tardor. Els volums de fosa es van restaurar només a la segona meitat de 1943.
La situació de refractaris a l'estructura del complex soviètic de defensa durant la Gran Guerra Patriòtica il·lustra clarament la complexitat de la situació a la rereguarda del país.
L’escassetat crònica, en general, del producte més avançat no va afectar directament el ritme de producció de vehicles blindats.