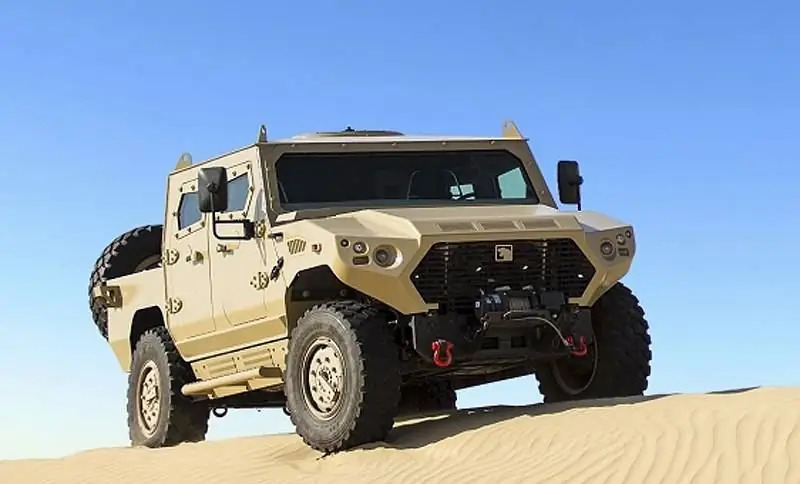
L’armadura té milions d’anys més que la humanitat i es va desenvolupar principalment per protegir-se contra les mandíbules i les urpes. És possible que els cocodrils i les tortugues puguin inspirar en part als humans a crear elements protectors. Totes les armes d'energia cinètica, ja sigui un club prehistòric o un projectil perforador d'armadura, estan dissenyades per concentrar força gran en una àrea petita, la seva tasca és penetrar a l'objectiu i causar-li el màxim dany. En conseqüència, la feina de l’armadura és evitar-ho desviant o destruint els mitjans d’atac i / o dispersant l’energia d’impacte per una àrea tan gran com sigui possible per minimitzar els danys a la mà d’obra, als sistemes de transport i a les estructures que protegeix.
Les armadures modernes normalment consisteixen en una capa exterior dura per aturar, desviar o destruir el projectil, una capa intermèdia amb un "treball per trencar" molt alt i una capa interna viscosa per evitar esquerdes i deixalles.
Acer
L’acer, que es va convertir en el primer material àmpliament utilitzat en la creació de vehicles blindats, encara és molt demandat, malgrat l’aparició d’armadures basades en aliatges lleugers d’alumini i titani, ceràmica, compostos amb matriu de polímers, reforçats amb fibres de vidre, aramida. i polietilè de pes molecular ultra alt, així com materials compostos amb matriu metàl·lica.
Moltes fàbriques d’acer, inclosa la SSAB, continuen desenvolupant acers d’alta resistència per a una gran varietat d’aplicacions de pes crític, com ara revestiments addicionals. L’armat d’acer blindat ARM OX 600T, disponible en gruixos de 4-20 mm, està disponible amb una duresa garantida de 570 a 640 unitats HBW (abreviatura de Duresa, Brinell, Wolfram; prova en què es prem una bola de tungstè d’un diàmetre estàndard en una mostra de material amb una força coneguda, es mesura el diàmetre del rebaix format; aquests paràmetres se substitueixen a la fórmula, que permet obtenir el nombre d’unitats de duresa).
SSAB també subratlla la importància d'assolir l'equilibri adequat de duresa i duresa per a la protecció contra penetració i explosió. Com tots els acers, ARMOX 600T es compon de ferro, carboni i diversos components d'aliatge, com ara silici, manganès, fòsfor, sofre, crom, níquel, molibdè i bor.
Hi ha limitacions en les tècniques de fabricació utilitzades, sobretot pel que fa a la temperatura. Aquest acer no està pensat per a un tractament tèrmic addicional; si s’escalfa a 170 ° C després del lliurament, SSAB no pot garantir les seves propietats. És probable que les empreses que puguin evitar aquest tipus de restriccions atreguin un estricte control dels fabricants de vehicles blindats.
Una altra empresa sueca, Deform, ofereix peces blindades resistents a les bales d'acer blindat a fabricants de vehicles blindats, en particular aquells que busquen millorar la protecció dels vehicles comercials / civils.
Els tallafocs Deform d’una sola peça s’instal·len al Nissan PATROL 4x4, al minibús Volkswagen T6 TRANSPORTER i a la camioneta Isuzu D-MAX, juntament amb una làmina sòlida del mateix material. El procés de formació en calent desenvolupat per Deform i utilitzat en la producció de xapes manté una duresa de 600HB [HBW].
L’empresa afirma que pot restaurar les propietats de tots els acers blindats del mercat mantenint una forma estructuralment definida, mentre que les parts resultants són molt superiors a les estructures tradicionals soldades i parcialment superposades. En el mètode desenvolupat per Deform, les làmines es treuen i temperen després de la forja en calent. Gràcies a aquest procés, és possible obtenir formes tridimensionals que no es poden obtenir mitjançant la formació en fred sense la obligatòria "soldadura que infringeix la integritat dels punts crítics".
S’han utilitzat xapes d’acer conformades en calent a BAE Systems BVS-10 i CV90 i, des de principis dels anys noranta, a moltes màquines Kraus-Maffei Wegmann (KMW). S’obtenen comandes per a la producció de plaques blindades tridimensionals per al tanc LEOPARD 2 i diverses plaques en forma per als vehicles BOXER i PUMA, a més de diversos vehicles Rheinmetall, incloent de nou el BOXER, així com una escotilla per al vehicle WIESEL. Deform també funciona amb altres materials de protecció com l'alumini, el kevlar / aramida i el titani.
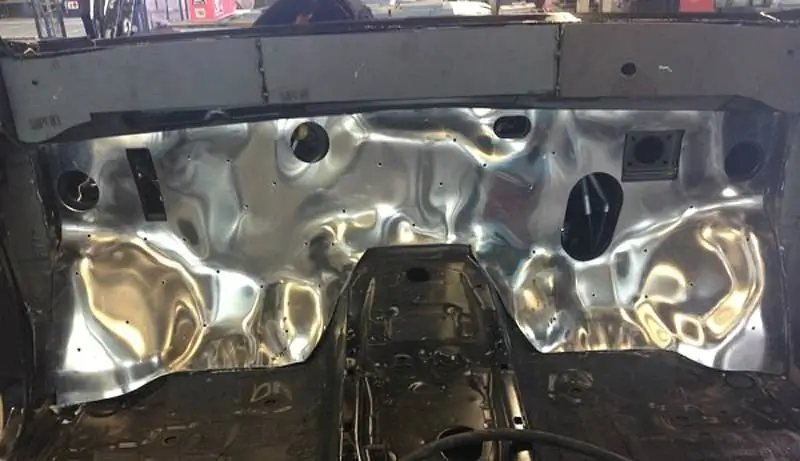
Progrés d'alumini
Pel que fa als vehicles blindats, per primera vegada es va utilitzar àmpliament l’armadura d’alumini en la fabricació del portaavions blindats M113, que es produeix des del 1960. Era un aliatge, denominat 5083, que contenia un 4,5% de magnesi i quantitats molt més petites de manganès, ferro, coure, carboni, zinc, crom, titani i altres. Tot i que el 5083 conserva bé la seva resistència després de la soldadura, no és un aliatge tractable tèrmicament. No té una resistència tan bona a les bales perforadores de 7,62 mm, però, segons van confirmar les proves oficials, atura les bales perforadores d’estil soviètic de 14,5 mm millor que l’acer, alhora que estalvia pes i afegeix la força desitjada. Per a aquest nivell de protecció, la xapa d’alumini és més gruixuda i 9 vegades més resistent que l’acer amb una densitat inferior de 265 r / cm3, cosa que redueix el pes de l’estructura.
Els fabricants de vehicles blindats aviat van començar a sol·licitar una armadura d’alumini més lleugera, més resistent, soldable i tractable tèrmicament, cosa que va conduir al desenvolupament d’Alcan del 7039 i posteriorment del 7017, ambdós amb un contingut de zinc superior.
Igual que amb l'acer, l'estampació i el posterior muntatge poden afectar negativament les propietats protectores de l'alumini. En soldar, les zones afectades per la calor es suavitzen, però la seva força es restaura parcialment a causa de l’enduriment durant l’envelliment natural. L'estructura del metall canvia en zones estretes properes a la soldadura, creant grans tensions residuals en cas d'errors de soldadura i / o muntatge. En conseqüència, les tècniques de fabricació haurien de minimitzar-les, mentre que també s’hauria de minimitzar el risc de fissuració per corrosió per estrès, especialment quan s’espera que la vida útil del disseny de la màquina sigui superior a tres dècades.
El cracking per corrosió per estrès és un procés d’aparició i creixement d’esquerdes en un entorn corrosiu, que tendeix a deteriorar-se a mesura que augmenta el nombre d’elements d’aliatge. La formació d’esquerdes i el seu posterior creixement es produeix com a resultat de la difusió de l’hidrogen al llarg dels límits del gra.
La determinació de la susceptibilitat a l’esquerda comença amb l’extracció d’una petita quantitat d’electròlit de les esquerdes i la seva anàlisi. Es realitzen proves de corrosió per esforç a baixa velocitat de deformació per determinar el grau de dany d’un aliatge concret. L’estirament mecànic de dues mostres (una en un entorn corrosiu i l’altra en aire sec) es produeix fins que fallen i, a continuació, es compara la deformació plàstica al lloc de la fractura; com més s’estira la mostra fins a fallar, millor.
Es pot millorar la resistència a la fissuració per corrosió per esforç durant el processament. Per exemple, segons Total Materia, que es fa dir "la base de dades de materials més gran del món", Alcan ha millorat el rendiment de 7017 en proves accelerades de craqueig per corrosió per estrès en 40 vegades. Els resultats obtinguts també permeten desenvolupar mètodes de protecció contra la corrosió per a zones d’estructures soldades, en les quals és difícil evitar esforços residuals. Les investigacions destinades a millorar els aliatges per optimitzar les característiques electroquímiques de les juntes soldades estan en curs. Els treballs sobre nous aliatges tractables per calor es centren en millorar la seva resistència i resistència a la corrosió, mentre que els treballs sobre aliatges no tractables per calor pretenen eliminar les restriccions imposades pels requisits de soldabilitat. Els materials més resistents en desenvolupament seran un 50% més forts que la millor armadura d’alumini que s’utilitza actualment.
Els aliatges de baixa densitat, com l’alumini de liti, ofereixen un estalvi de pes del 10% respecte als aliatges anteriors amb una resistència de bala comparable, tot i que el rendiment balístic encara no s’ha avaluat completament segons Total Materia.
Els mètodes de soldadura, inclosos els robotitzats, també estan millorant. Entre les tasques que es resolen hi ha la minimització del subministrament de calor, un arc de soldadura més estable a causa de la millora dels sistemes d’alimentació d’energia i filferro, així com el control i control del procés per part de sistemes experts.
MTL Advanced Materials va treballar amb ALCOA Defense, un reconegut fabricant de plaques blindades d'alumini, per desenvolupar el que la companyia descriu com un "procés de formació en fred fiable i repetible". L'empresa assenyala que els aliatges d'alumini desenvolupats per a aplicacions d'armadures no van ser dissenyats per a la formació en fred, de manera que el seu nou procés hauria d'ajudar a evitar modes de fallada habituals, inclosa la fissuració. L'objectiu final és permetre als dissenyadors de màquines minimitzar la necessitat de soldadura i reduir el nombre de peces, segons la companyia. La companyia redueix el volum de soldadura, subratlla, augmenta la resistència estructural i la protecció de la tripulació alhora que redueix els costos de producció. Començant per l’aliatge 5083-H131, provat, l’empresa va desenvolupar un procés per formar peces en fred amb un angle de flexió de 90 graus al llarg i a través dels grans, i després va passar a materials més complexos, per exemple, els aliatges 7017, 7020 i 7085, aconseguint també bons resultats.
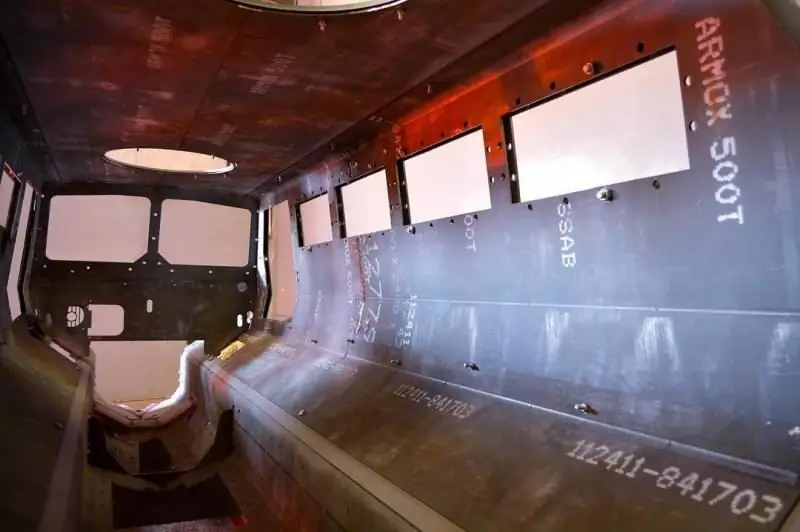
Ceràmica i composites
Fa diversos anys, Morgan Advanced Materials va anunciar el desenvolupament de diversos sistemes de blindatge SAMAS, que consistien en una combinació de ceràmica avançada i compostos estructurals. La línia de productes inclou armadures articulades, revestiments antifragmentació, càpsules de supervivència fabricades amb compostos estructurals per substituir cascos metàl·lics i protegir mòduls d’armes, tant habitats com deshabitats. Tots ells es poden adaptar a requisits específics o fer-los per encàrrec.
Proporciona protecció STANAG 4569 Nivell 2-6, juntament amb un rendiment multi-impacte i un estalvi de pes (la companyia afirma que aquests sistemes pesen la meitat que productes similars d’acer) i s’adapten a amenaces, plataformes i missions específiques … Els revestiments anti-estella es poden fer a partir de panells plans que pesen 12,3 kg per cobrir una superfície de 0,36 m2 (uns 34 kg / m2) o accessoris sòlids que pesen 12,8 kg per 0,55 m2 (uns 23,2 kg / m2).
Segons Morgan Advanced Materials, les armadures addicionals dissenyades per a la nova i la modernització de plataformes existents ofereixen les mateixes capacitats a la meitat del pes. El sistema patentat proporciona la màxima protecció contra una àmplia gamma d’amenaces, incloses les armes de petit i mitjà calibre, els dispositius explosius improvisats (IED) i les magranes propulsades per coets, així com el rendiment de múltiples impactes.
S'ofereix un sistema d'armadura "semi-estructural" amb bona resistència a la corrosió per als mòduls d'armes (a més d'aplicacions aèries i marítimes), juntament amb l'estalvi de pes i la minimització de problemes amb el centre de gravetat, a diferència de l'acer, crea menys problemes de compatibilitat electromagnètica.
La protecció dels mòduls d'armes és un problema particular, ja que són un objectiu atractiu, ja que la seva inhabilitació afecta dràsticament el domini de la situació de la tripulació i la capacitat del vehicle per fer front a amenaces properes. També tenen optoelectrònica delicada i motors elèctrics vulnerables. Com que normalment s’instal·len a la part superior del vehicle, l’armadura ha de ser lleugera per tal de mantenir el centre de gravetat el més baix possible.
El sistema de protecció dels mòduls d’armes, que pot incloure vidre blindat i protecció de la part superior, és completament plegable, dues persones el poden tornar a muntar en 90 segons. Les càpsules de supervivència compostes es fabriquen amb el que la companyia descriu com a "materials resistents únics i formulacions de polímers", que proporcionen protecció contra metralles i es poden reparar al camp.
Protecció de soldat
El sistema SPS (Soldier Protection System) desenvolupat per 3M Ceradyne inclou cascos i insercions en armadures per als components del Sistema Integrat de Protecció del Cap (IHPS) i VTP (Vital Torso Protection) - Components ESAPI (Enhanced Small Arms Protective Insert) - Inserció millorada armes petites) del sistema SPS.
Els requisits IHPS inclouen un pes més lleuger, protecció auditiva passiva i una millor protecció contra els impactes contundents. El sistema també inclou accessoris com ara un component per protegir la mandíbula inferior d’un soldat, una visera protectora, un suport per a ulleres de visió nocturna, guies per, per exemple, llanterna i càmera, i protecció modular addicional contra bales. El contracte, per valor de més de 7 milions de dòlars, preveu el subministrament d’uns 5.300 cascos. Mentrestant, es lliuraran més de 30.000 kits ESAPI (insercions més lleugeres per a armadures) segons el contracte de 36 milions de dòlars. La producció d’aquests dos kits va començar el 2017.
També dins del programa SPS, KDH Defense va seleccionar els materials SPECTRA SHIELD i GOLD SHIELD de Honeywell per a cinc subsistemes, inclòs el subsistema Torso and Extremity Protection (TEP) que es subministraria per al projecte SPS. El sistema de protecció TEP és un 26% més lleuger, cosa que redueix el pes del sistema SPS en un 10%. KDH utilitzarà SPECTRA SHIELD, que es basa en fibra UHMWPE, i GOLD SHIELD, basat en fibres d’aramida, en els seus propis productes per a aquest sistema.
Fibra SPECTRA
Honeywell utilitza un procés propietari de filat i estirat de fibra polimèrica per incrustar la matèria primera UHMWPE a la fibra SPECTRA. Aquest material és 10 vegades més fort que l’acer en termes de pes, la seva resistència específica és un 40% superior a la de la fibra aramida, té un punt de fusió més alt que el polietilè estàndard (150 ° C) i una major resistència al desgast en comparació amb altres polímers, per a per exemple, el polièster.
El material SPECTRA fort i rígid presenta una alta deformació en trencar-se, és a dir, s’estén molt fort abans de trencar-se; aquesta propietat permet absorbir una gran quantitat d'energia d'impacte. Honeywell afirma que els compostos de fibra SPECTRA funcionen molt bé sota impactes a gran velocitat, com ara bales de rifles i ones de xoc. Segons l’empresa, “la nostra fibra avançada reacciona a l’impacte eliminant ràpidament l’energia cinètica de la zona d’impacte … també té un bon amortiment de les vibracions, una bona resistència a deformacions repetides i unes excel·lents característiques de fregament intern de les fibres juntament amb una excel·lent resistència als productes químics., aigua i llum UV."
En la seva tecnologia SHIELD, Honeywell estén fils de fibres paral·lels i els uneix impregnant-los amb una resina avançada per crear una cinta unidireccional. A continuació, les capes d'aquesta cinta es col·loquen transversalment en els angles desitjats i a una temperatura i pressió determinades, soldades en una estructura composta. Per a aplicacions suaus de portar, es laminen entre dues capes de pel·lícula transparent fina i flexible. Com que les fibres es mantenen rectes i paral·leles, dissipen l'energia d'impacte de manera més eficient que si es teixissin en un teixit.
Short Bark Industries també utilitza SPECTRA SHIELD al guardaespatlles BCS (Ballistic Combat Shirt) per al sistema SPS TEP. Short Bark està especialitzada en protecció suau, roba tàctica i accessoris.
Segons Honeywell, els soldats van triar elements de protecció fets d'aquests materials després de demostrar un rendiment superior als seus homòlegs de fibra aramida.