El patriotisme de l’elit industrial soviètica es va combinar amb la responsabilitat conjunta del resultat final
La interacció interindustrial en tot moment -tant a l’Imperi rus com a l’URSS i avui- no pertanyia als punts forts de la indústria nacional. En contrast amb Alemanya o els Estats Units, on les obligacions contractuals tenien i tenen una força immutable i gairebé sagrada.
Prenem, per exemple, la relació entre metal·lúrgics russos i constructors de màquines. A la segona meitat del segle XIX, les noves plantes d’enginyeria de transport i les drassanes no van rebre la quantitat necessària de metalls industrials dels miners d’Ural. Aquests últims van considerar que no era rendible fabricar molts productes laminats relativament barats, ja que el mateix benefici el proporcionava un volum molt més reduït de ferro car per a sostres. El metall que faltava per als eixos del cotxe, els eixos del motor i la pell del vaixell s’havia de comprar a l’estranger. Només a finals de segle, el problema va ser resolt per les plantes metal·lúrgiques del sud de Rússia, fundades per industrials belgues o francesos. Als Urals, els francesos també van construir una planta: Chusovskaya.
Semblaria que a l’època soviètica aquests capricis eren fora de qüestió. A més, les plantes metal·lúrgiques construïdes als anys 30 van proporcionar al país el metall en el seu conjunt. No obstant això, cada vegada que els fabricants de màquines sol·licitaven nous tipus complexos de productes laminats, els metal·lúrgics els dominaven durant anys o fins i tot dècades.
Feudalisme departamental
Passem a la història d’Uralvagonzavod. Ja en els seus primers projectes, es preveia utilitzar rodes d’acer laminat sòlid sota els cotxes de quatre eixos a mesura que la capacitat de disseny arribava a la seva capacitat de disseny, el proveïdor del qual estava previst per a la propera planta metal·lúrgica de Novo-Tagil. Tanmateix, aquesta última estava sent construïda pel departament metal·lúrgic i va ajornar la construcció del laminador de rodes al 1938-1942, i no en primer lloc. Com a resultat, el cas no va començar abans de la guerra. I després de la guerra, el lloguer de rodes no va estar massa interessat pels metal·lúrgics. Resultat: fins a mitjans dels anys 50, els cotxes Tagil van abandonar la fàbrica amb rodes de ferro colat de curta durada en lloc d’unes d’acer. Això va comportar grans pèrdues per als treballadors del ferrocarril, però no hi va haver altra opció: o bé aquests cotxes o cap.
El mateix va passar amb la introducció d’acers de baixa aliatge a la construcció de carros. Van prometre una reducció notable del pes mort del material mòbil tot mantenint totes les característiques de rendiment. Els dissenyadors d’Uralvagonzavod van començar a dissenyar cotxes de metall de baixa aliatge a finals dels anys 30, però la seva producció en sèrie només va començar a la segona meitat dels anys 50, ja que els metal·lúrgics no proporcionaven ni productes laminats ni ferroaliatges adequats per a la fosa de peces.
Cal dir que el virus del feudalisme departamental va afectar els mateixos constructors de màquines. L’estiu de 1937 va tenir lloc una interessant història que va caracteritzar les relacions interinstitucionals d’aquella època. La Direcció Principal d'Empreses Metal·lúrgiques va enviar a Uralvagonzavod una comanda de cinc mil tones de blancs per a la fàbrica de vendes recentment llançada de la planta de Novo-Tagil. La Direcció Principal d'Enginyeria del Transport es va mostrar indignada per la violació d'una empresa subordinada. Cap adjunt de la Direcció Principal G. G. L’11 de juliol, Aleksandrov va enviar una carta a GUMP i Uralvagonzavod amb la següent afirmació: “Ens sorprèn molt que la solució d’un tema tan important com l’organització de la producció d’un embenat en blanc a Uralvagonzavod es dugués a terme sense la nostra participació, i més encara - Ni tan sols ens van enviar una còpia del vestit enviat a Uralvagonzavod … Us demano que estableixi un procediment ferm per emetre espais en blanc a les nostres fàbriques només per acord amb nosaltres i a través de Glavtransmash."
Com a resultat, als metal·lúrgics se'ls va negar l'embenat d'acer, presumptament a causa de la impossibilitat tècnica de llançar lingots d'alta qualitat a la botiga oberta de l'Uralvagonzavod. Mentrestant, ja el 1936, es va emetre un buit axial aquí i el 1937 - lingots per laminar xapes. Per tant, els lingots per al molí sudari, situat a pocs quilòmetres de la UVZ, van haver de ser transportats des de les plantes de Vyksa i Kuznetsk. A més, la seva qualitat deixava molt a desitjar i els volums de subministraments eren insuficients.
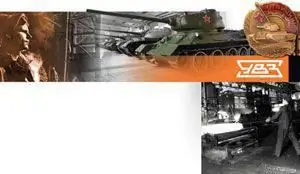
El 1938, la història es va repetir. El principal consumidor de lingots UVZ va ser la planta d’artilleria Molotov (és a dir, Perm), que va rebre un lot d’espais en blanc a finals d’any. I només un petit nombre d’ells van anar a la botiga d’embenats, que de nou va haver d’importar el metall que faltava durant dos o dos mil quilòmetres i mig. Els interessos de la indústria en la distribució de l’acer Uralvagonzavodsk van prevaler clarament.
La malaltia departamental tampoc va estalviar la indústria de la defensa. Nombroses publicacions sobre la història de la construcció de tancs soviètics estan completament repletes d’exemples de com es va retardar la construcció de prototips o el desplegament de la producció en massa a causa del no lliurament de metall, especialment d’armadures.
I encara avui l’interès sectorial no ha anat enlloc, només ha canviat la seva forma. Les sol·licituds de noves formes de productes enrotllats es combaten simplement amb preus desorbitats. No cal parlar d’una política coordinada. Després del col·lapse del tipus de canvi del ruble a finals de 2014-2015, les empreses metal·lúrgiques van augmentar els preus del material mòbil en un 30-60 per cent. I de seguida van començar a queixar-se dels fabricants de màquines pels equips que havien augmentat el preu; al cap i a la fi, les màquines es produeixen a Rússia i no estan relacionades amb el tipus de canvi del dòlar.
Sembla que al nostre país només hi ha una cura per als problemes intersectorials: la creació de sistemes integrats verticalment, on el mineral extret per les nostres pròpies forces es converteix primer en metall i després en màquines acabades.
Unitat de guerra
Tanmateix, hi ha un breu període en la nostra història en què els interessos de la indústria han retrocedit en un segon pla. Estem parlant de la Gran Guerra Patriòtica. El patriotisme indubtable de l’elit industrial soviètica en aquella època es combinava amb la responsabilitat conjunta de tots els implicats en la producció de defensa pel resultat final. És a dir, el director de la planta de laminació blindada era responsable no tant del volum d’acer fos i laminat, sinó del nombre de tancs construïts.
El pas principal en aquesta direcció el va fer el director de NII-48 A. S. Zavyalov. Els primers dies de la guerra, es va dirigir al govern amb una proposta d’instrucció a l’institut per introduir tecnologies per a la producció d’acers especials i estructures blindades a les empreses de l’est del país, que van participar per primera vegada en la fabricació de blindats. vehicles. A principis de juliol, equips d'especialistes de NII-48 van encapçalar la reestructuració tecnològica de 14 empreses més grans. Entre elles es trobaven les plantes metal·lúrgiques Magnitogorsk i Kuznetsk, les plantes metal·lúrgiques Novo-Tagil i Chusovka, la planta de construcció de màquines pesades d’Ural, la planta de tractors de Gorky Krasnoye Sormovo, la planta de tractors de Stalingrad, l’octubre vermell de Stalingrad i el número 264. Així, Zavyalov va violar la tabú d’abans de la guerra: la llista incloïa empreses de comissariats de tres persones.
El patriotisme i la supressió obligatòria de l'egoisme departamental van proporcionar a la metal·lúrgia soviètica índexs de desenvolupament de productes de defensa sense precedents, ni en la pre-guerra ni en la postguerra. En qüestió de mesos, a l'est del país (principalment als Urals) es va organitzar la producció de ferromanganès, ferrosilici, ferrocrom, ferrovanadi i altres aliatges, sense els quals és impossible obtenir acer blindat. Després de la pèrdua de les regions occidentals, Chelyabinsk va continuar sent l'única planta de ferroaliatges de l'URSS. En ella, en poc temps, la fosa es va augmentar dues vegades i mitja. Es van produir 25 tipus de productes, però sobretot eren de diversos tipus de ferrocrom. La fosa del ferromanganès es va establir als alts forns, i no només als alts forns antics de baix tonatge de les plantes de Nizhniy Tagil i Kushvinsky, sinó també en un gran forn modern de la combinació Magnitogorsk. Contràriament a totes les idees d’abans de la guerra, el ferrocrom va ser fondut a la segona meitat de 1941 pels seus alts forns per metal·lúrgics de les plantes de Nizhniy Tagil i Serov, i científics de la branca Ural de l’Acadèmia de Ciències de l’URSS van proporcionar una gran ajuda per crear un nou tecnologia. Més tard, la fosa de ferrosilici es va dominar als alts forns de Serov.
No hi havia camps blindats ni als Urals ni a Sibèria Occidental abans de la guerra, havien de ser transferits a corre-cuita de les empreses que es trobaven a la zona de combat.
L'estiu de 1941, l'equipament evacuat encara estava en trànsit. I després, el mecànic principal de la combinació Magnitogorsk, N. Ryzhenko, va suggerir rodar l’armadura sobre un molí en flor. Tot i el gran risc, la idea es va dur a terme. I a l’octubre va entrar en servei un campament blindat, extret de la planta de Mariupol. Es va muntar en només 54 dies. Segons els estàndards d’abans de la guerra, això va trigar un any.
La planta de Novo-Tagil va aconseguir el campament de Leningrad. Els preparatius per a la seva admissió van començar al juliol, inicialment es va suposar que es muntaria al lloc de l'embenat. El campament de vendes es va desmuntar, però va resultar que el vell estoc no era suficient per instal·lar el camp blindat i que s’havia de col·locar en un altre lloc. La guerra va obligar a fer allò que es considerava impossible fins fa poc: fa tot just un any, els intents de dur a terme la construcció industrial mitjançant un mètode integrat "d'alta velocitat" a Nizhny Tagil van tenir, com a molt, un èxit parcial, i l'estiu de 1941 el més important la complexa operació de construcció era gairebé perfecta. El 10 de setembre es va enrotllar la primera xapa d’acer Tagil un mes abans del previst. En total, a finals d’any es van obtenir 13.650 tones de xapa, incloent-hi aproximadament el 60% de l’armadura (el molí es va provar amb acer al carboni i, entre octubre i desembre, l’acer al carboni es va laminar amb una escassetat de lingots d’armadura). Com a resultat, ja al gener de 1942, la producció mensual de plaques d’armadura a les fàbriques d’Ural va superar els sis mesos a tota la Unió Soviètica d’abans de la guerra.
No es van produir fets menys sorprenents en altres empreses poc conegudes. Durant la guerra, la planta metal·lúrgica de Zlatoust va ser inferior a la combinació Magnitogorsk pel que fa al volum de fosa i acer laminat, però la va superar significativament en la seva combinació de productes: aquí es van produir uns 300 graus d’aliatge i acer al carboni. Sense els subministraments de Zlatoust, la producció de molts tipus d’armes, principalment motors de tanc, s’hauria aturat.
Les antigues fàbriques d’Ural van resultar indispensables per a la producció de petits lots d’acer d’alta qualitat. Per exemple, el metall de Serov Metallurgical, el principal fabricant de productes laminats calibrats, es va invertir en tots els tancs soviètics. La planta de Nizhnesalda va passar a la fosa de ferro i acer de níquel. Aquesta llista es pot continuar sense parar: durant els anys de la guerra, allà on hi hagués almenys una cúpula, es va fondre el metall de qualitat.
Hi ha una curiosa història amb fluxos de soldadura automàtica. Abans i al començament de la guerra, es van fondre en una de les empreses de Donbass, després de l'ocupació de la qual es van aturar completament els subministraments centralitzats. A finals de 1941, els empleats de l’Institut de Soldadura Elèctrica de l’Acadèmia de Ciències de la RSS d’Ucraïna van començar a buscar materials substitutius disponibles als Urals en un estat més o menys útil. I els van trobar, en forma d’escòries de l’alt forn de la planta metal·lúrgica Ashinskiy. Només es necessitaven petites millores: els alts forns van enriquir les seves escòries amb manganès i, per tant, les van convertir en un flux completament adequat. L'equip necessari per a les proves va ser portat de Nizhny Tagil directament a Asha.
Els exemples de cooperació local entre tancs i plantes metal·lúrgiques són molt indicatius. Abans del llançament de les seves pròpies instal·lacions, es realitzava un tractament tèrmic de les parts del tanc de la planta de dipòsits Ural núm. 183 a la planta metal·lúrgica de Nizhniy Tagil.
L’èxit del treball dels treballadors de la foneria UTZ es va veure molt facilitat per l’assistència de la veïna planta de petard de Nizhniy Tagil, que va establir la producció de taps de sílex de parada refractària d’alta qualitat. Això va fer possible la colada sense problemes de foses pesades d'acer blindat per a la colada en forma.
El 1942-1945, els forns oberts a UTZ funcionaven principalment amb gas de forn de coc i alt forn de les plantes de coc de Novo-Tagil Metallurgical i Nizhniy Tagil. El gasoducte funciona des del febrer de 1942. La pròpia central de generació de gas de la planta núm. 183 no proporcionava més del 40% de les necessitats.
De vegades, un simple consell era suficient per resoldre un problema. La informació dels metal·lúrgics locals sobre una petita mina de manganès desenvolupada a la dècada de 1870 va ajudar a sobreviure diverses setmanes abans de l’inici dels lliuraments de ferromanganès sense aturar la colada de pistes de tancs.
Un altre exemple: a mesura que augmentava la producció d'acer blindat, la botiga oberta ja no podia seguir el ritme de la fosa de metall per als caps de les bombes aèries. No era possible aconseguir-ho des de fora. El director Yu, E. Maksarev, va recordar el curs d’altres esdeveniments a les seves memòries: “Quan estava en una de les reunions del comitè de la ciutat, vaig conèixer el director de l’antiga planta, encara Demidov, i vaig demanar que em fes el càsting de els caps de la bomba. Va dir: No puc ajudar amb l’acer, però amb consells l’ajudaré. I quan vaig arribar a la seva planta, em va ensenyar un convertidor Bessemer d’una tona i mitja amb bufat mitjà. Em va donar els dibuixos i em va dir que sap que tenim una bona foneria de ferro mecanitzada i els seus convertidors es soldaran”. Així va aparèixer l’ordre de la planta del 8 de setembre de 1942 a l’organització a la botiga de rodes Griffin de la secció Bessemer de tres petits convertidors (una i mitja de metall cadascun). El 25 de setembre, el projecte va ser preparat pel departament de disseny i tecnologia de la direcció de la construcció de capitals, els especialistes del departament del cap de mecànics van soldar ràpidament convertidors i calderes: dipòsits d’emmagatzematge de ferro líquid. La prova del departament de Bessemer i el repartiment d’un lot experimental de cinc noms de peces van tenir lloc a finals d’octubre-novembre de 1942. La producció en sèrie va començar a finals de novembre.
Al final del tema: la cooperació de metal·lúrgics i constructors de tancs en temps de guerra va actuar en ambdues direccions. Els instal·ladors de la planta de tancs d’Ural van participar en la posada en servei de moltes unitats noves de la planta metal·lúrgica de Novo-Tagil. Al maig de 1944, es va fabricar un nombre important de plaques de revestiment per a la reparació de l’alt forn a la botiga de fosa de torre blindada.
Però el principal ajudant dels metal·lúrgics era, per descomptat, la planta de construcció de màquines pesades d’Ural. Els llibres de comandes per a UZTM del 1942 al 1945 estan literalment empaquetats amb documents sobre la producció de recanvis i dispositius per a propòsits metal·lúrgics, tant per a les necessitats de la indústria de tancs com per a les empreses del Comissariat del Poble de Metal·lúrgia Ferrosa. A la tardor de 1942, es va restaurar oficialment a UZTM una divisió especial per a la producció d’equips per a plantes metal·lúrgiques. Va rebre el codi "Divisió 15" i estava subordinat al subdirector de botigues de compres i producció de casc.
Èxit a la intersecció d’indústries
La cooperació de metal·lúrgics i constructors de tancs ha conduït a la creació d’una sèrie de tecnologies que, sense exageracions, es poden anomenar autèntics avenços científics i tècnics.
Després d’haver fos i laminat l’acer blindat en xapes, els metal·lúrgics van transferir els seus productes a la producció de casc blindat. Aquí es va tallar el metall segons la plantilla en les parts corresponents. En la producció de "trenta-quatre", sobretot dues molèsties del casc van provocar molts problemes: defenses (el costat inclinat del costat) i la placa lateral vertical. Tots dos eren llargs, fins i tot en tires d’amplada amb talls oblics a les vores.
La idea, naturalment, es va suggerir fer rodar una tira de mesura d’amplada igual a les parts acabades. Va ser formulat per primera vegada pels cotxes blindats de la planta de Mariupol l’estiu de 1941. Per al rodatge de proves, vam escollir un molí de forjat a Zaporizhstal, on es van enviar dos esglaons de lingots d’armadura. Però després no van tenir temps de posar-se a treballar: les tropes alemanyes que van avançar van capturar tant els esglaons com el propi Zaporozhye.
Al tombant de 1941-1942, durant l'evacuació i el desenvolupament de la producció d'armadures a les noves fàbriques, no hi havia prou franja. Tanmateix, el maig de 1942, el Comissariat Popular de Metal·lúrgia Ferrosa va rebre novament una ordre de lloguer per a tancs T-34 i KV. La tasca va resultar difícil: les toleràncies d'amplada no haurien de superar els -2 / + 5 mil·límetres, la forma de mitja lluna (corba) de la longitud total de la peça era de 5 mil·límetres. No es permetien esquerdes, capvespres ni delaminacions a les vores, de manera que es podia dur a terme soldadures sense mecanitzar ni tallar flames.
Els treballs experimentals van començar simultàniament a les botigues rodants de les plantes metal·lúrgiques de Magnitogorsk i Kuznetsk, al principi sense assoliments particulars. El lloguer de peces per als tancs KV aviat va ser abandonat, però el T-34 finalment va tenir èxit. L’equip d’autors format pel cap del departament metal·lúrgic de la NII-48 G. A. Vinogradov, l’enginyer en cap de la KMK L. E. Vaisberg i l’enginyer de la mateixa planta S. E. es troba al "900" del molí ferroviari i estructural. mètode de rodar "a la vora". El gener de 1943 es van emetre 280 tires, al febrer - 486, al març - 1636 peces. A l'abril, després de totes les proves necessàries, es va iniciar el desenvolupament de la producció bruta de tires de mesura per als revestiments de passos de rodes dels tancs T-34. Inicialment, es subministraven a UZTM i la planta de tancs d’Ural, i després a altres fàbriques, fabricants de tancs T-34. La ferralla, que inicialment tenia un 9,2%, havia caigut al 2,5% a l’octubre de 1943 i les tires inferiors s’utilitzaven per fabricar peces més petites.
El corresponent informe de TsNII-48 de 25 de desembre de 1943 dóna una avaluació completa i precisa de la nova tecnologia: "Es va desenvolupar, provar i introduir a la producció bruta un mètode fonamentalment nou de fer rodar una banda blindada ampla" a la vora "., que es considerava inviable fins fa poc a l’URSS i a l’estranger. L’obtenció d’una tira calibrada (mesurada) amb una amplada de la part acabada del casc blindat del tanc T-34 va fer possible que les fàbriques NKTP adoptessin una nova tecnologia d’alt rendiment per a la fabricació de peces blindades sense tallar vores longitudinals. Gràcies a l'aplicació del nou mètode a una de les parts blindades principals del tanc T-34 (parabolts), es va aconseguir un estalvi de temps molt significatiu (al voltant del 36%) en tallar-los. Es va aconseguir un estalvi d’acer blindat 8C fins a un 15 per cent i un estalvi d’oxigen de 15.000 cbm per cada 1000 bucs”.
A finals de 1943, es va dominar el rodament d’una tira de mesura per a una altra part del casc T-34: la part vertical del lateral. Només queda afegir que els autors d’aquest invent van rebre el Premi Stalin el 1943.
El mateix 1943, gràcies als esforços conjunts del laboratori de l’Institut Ucraïnès dels Metalls (dirigit per PA Aleksandrov) i dels treballadors de la combinació metal·lúrgica de Kuznetsk i de la planta de tancs d’Ural, es va desenvolupar un perfil laminat periòdic especial que es va dominar en la producció per a l’adquisició. de la massa i les parts crítiques dels "trenta-quatre": eixos equilibradors. El primer lot experimental d'un perfil periòdic es va rebre a KMK al desembre, a principis de 1944, va començar la producció en sèrie. A l’octubre, la planta de tancs d’Ural va canviar completament a la fabricació d’eixos equilibradors a partir d’un nou buit, a finals d’any UZTM s’hi va unir. Com a resultat, la productivitat dels forjadors va augmentar un 63 per cent i el nombre de trencaments de peces va disminuir.
L’èxit del treball dels constructors de tancs va ser molt facilitat pel material rodant del molí d’embenat de la planta metal·lúrgica de Novo-Tagil. A partir de la primavera de 1942, van subministrar tirants rodats amb reduccions de la quantitat de mecanitzat; el 1943 es van reduir de nou les quotes. En combinació amb la nova eina de tall, això va permetre dur a terme un despullament que requereix molt de temps de les corretges d’espatlla estrictament en el temps previst i sense molta tensió. Un cas rar: el comissari popular de la indústria de tancs V. A. Malyshev, en la seva ordre del 28 de setembre de 1943, va considerar necessari expressar un agraïment especial als metal·lúrgics tagil.
I, finalment, el darrer exemple: el 1943, les llantes dels tancs de suport T-34, primer a la planta de Chelyabinsk Kirov, i després a altres empreses, van començar a fabricar-se amb productes laminats de perfil especial. Aquest èxit també es va notar en l'ordre de V. A. Malyshev.
Cal afegir que els especialistes de l’empresa nord-americana "Chrysler", després d’haver estudiat el tanc T-34-85 capturat a Corea, van assenyalar especialment la perfecció dels espais en blanc a partir dels quals es va fabricar el vehicle de combat. I també el fet que sovint superaven els productes de les empreses metal·lúrgiques dels Estats Units.